“Our vision is to make guitars that are treated more like gear than fine art, or delicate furniture at grandma’s house’’: Charging full speed ahead with carbon-fiber designs, the founders of Klos Guitars believe guitars should be used, not babied
Klos co-founders Adam and Ian Klosowiak are all in on creating a unique array of carbon-fiber instruments fit for an adventurous lifestyle
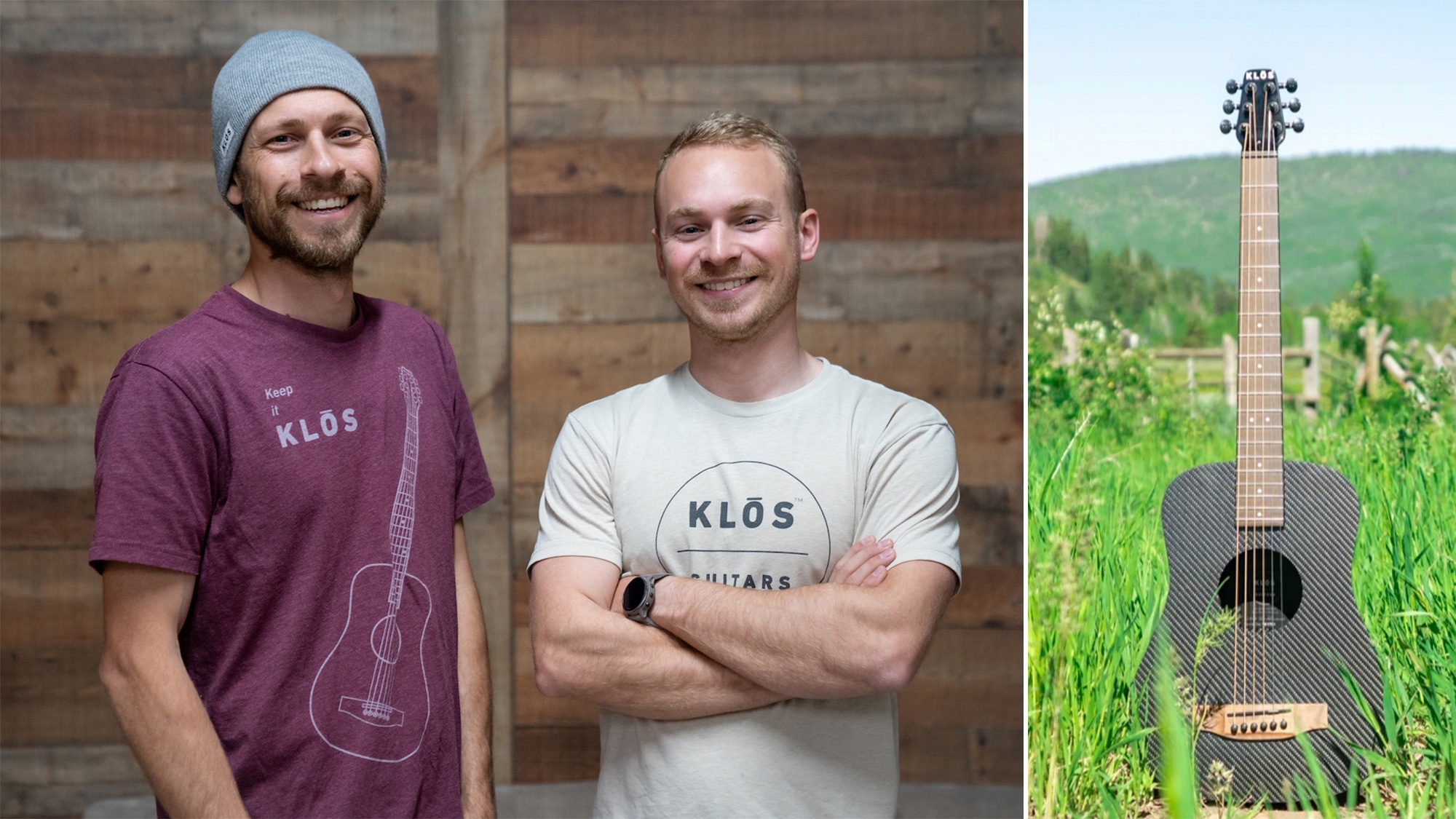
The carbon-fiber revolution may not be televised, but it’s all over the internet and here in the pages of GP.
The young Klosowiak brothers bring a unique perspective, focused on intelligent builds using modern materials in traditional forms. They make sonorous and highly playable carbon instruments at lower prices than other custom manufacturers, and market them to adventure lifestylists, who benefit most from the resulting durability. Their ads feature Klos guitars on the backs of hikers and sailors, and hilarious online videos show players using their wares as golf clubs and baseball bats.
A successful Kickstarter campaign for the Travel Guitar put Klos (pronounced like the opposite of “far”) on the map in 2015. The 33-inch miniature dreadnought remains the company’s flagship, but Klos has expanded the line significantly and now offers a fleet of acoustic and electric instruments in an array of sizes up to the full-scale Grand Cutaway. Last month, their three-quarter-sized Grand Cutaway Mini acoustic-electric earned an Editors’ Pick review for being travel-friendly and gig-worthy.
Klos is currently introducing an A-style mandolin, a nylon-string, and a 12-string with a particularly cool tuning-peg design on its headstock to go along with a full line of basses and ukuleles. The company offers lots of custom options for each. The Hybrid Series combines wood and carbon and is more affordable, while Carbon Timber is an intriguing newfangled material that doesn’t contain any wood but has a straight grain appearance rather than the traditional carbon-fiber weave.
I caught up with Klos at the NAMM show and was impressed with the consistency in craftsmanship across its expanding range of instruments. With so much goodness coming down the mountain from Provo, Utah, it’s high time we met the brothers behind the brand.
What was the big bang that brought Klos Guitars into the universe?
Ian Klosowiak: “I was studying mechanical engineering at Brigham Young University and built a carbon-fiber guitar for a class. It was a lifelong goal to build a guitar of my own. During the process I did a ton of research and recognized that there was no company making carbon-fiber guitars at a reasonable price in a high-end, yet practical way.”
Get The Pick Newsletter
All the latest guitar news, interviews, lessons, reviews, deals and more, direct to your inbox!
Adam Klosowiak: “Soon after, I was visiting Ian when he asked if I knew anything about business competitions. I had won a hackathon at Princeton the year before, where I studied electrical engineering.”
Ian: “Adam was involved with entrepreneurship, so we decided to put our heads together and start a company making a new category of guitars that you can depend on.”
Were you inspired by any brands or models?
Ian: “I was inspired by a bunch of guitars, but being an avid mountain biker, the main inspiration came from the mountain bike industry. I credit my knack for working with tools and being detail oriented, as well as my experience as a bike mechanic. Over the past two decades, carbon fiber has become increasingly popular for making mountain bikes. I believe the same thing will happen with guitars, because there are so many advantages over wood.”
What got you hooked on carbon fiber in the first place?
Ian: “My first exposure to making carbon-fiber parts was during an internship in a carbon-fiber lab at Northwestern University. After learning the basics, I successfully fixed a couple of carbon-fiber bike frames, and I made a bunch of random things for fun. I got familiar with Rainsong’s highly coveted carbon guitars, but they’re expensive and out of range for a college student.
“Living in Utah and Colorado, naturally I did a lot of camping, rock climbing, skiing, and mountain biking, and I brought my guitar everywhere. Seeing my wood guitar get beat up from all the travel, I started obsessing about owning a carbon-fiber guitar one day. At the same time, while Adam was a student at Princeton, his guitar developed a crack in the soundboard simply from sitting next to an open window. Since both of us were experiencing the same pain points, we knew there was an opportunity with carbon-fiber guitars.”
Durability is a primary advantage, but are there sonic advantages as well?
Adam: “People have created stereotypes about carbon fiber and make a lot of assumptions about its sound. Like wood, carbon fiber can be designed and modified to have a wide range of sonic properties. We can make guitars that sound bright, and some have very deep bass, but in general we always aim to have a balanced tone.
“Aside from good sound, our instruments have excellent playability, which is something we pride ourselves on. We spend hours and hours on each instrument, making sure it does not leave our shop until we’re confident the customer will find the playability to be the best they’ve ever experienced.”
Most carbon-fiber makers go with an offset soundhole, yet yours is traditional, and you offer a side sound port as a custom option.
Adam: “Nice observation. We try to innovate on top of tradition, and because our material is already very innovative, we try to keep other elements of the instruments traditional whenever possible. We therefore have traditional soundholes, but we do offer side sound ports for players who want it. A side sound port on an acoustic instrument works like a monitor for the player and makes an instrument sound much louder for the person playing.”
Ian: “Our most popular customization is the choice of pickup. You can achieve a specific sound by choosing the pickup you know and love, such as the Baggs and Fishman pickups we offer for acoustics. Or we can do a custom install of whatever you send us. We also offer the HyVibe smart guitar preamp. For electric and bass guitar, we have a unique pickguard that can pretty much handle any pickups, with any type of knob configuration. Our pickguards are fully loaded, so if you ever want a new pickup or layout, it’s not a problem.”
What’s the deal with Carbon Timber?
Adam: “Carbon Timber is incredible. The material is nickel-coated carbon fiber, so the carbon strands have nickel atoms coated on top of them. The result is a material that is as incredibly durable as black carbon fiber but has a brown, metallic wood-like appearance. The Carbon Timber strands are laid in one direction, and the resulting grain makes each instrument unique. We’re very excited about it and have seen a huge positive response from customers thus far.”
What makes the Travel Guitar the most popular and lauded of your instruments?
Adam: “Carbon fiber’s durability makes it a perfect fit because travel guitars undergo the most stress. We made only Travel Guitars for the first three years, so that product line had a head start. It has substantially more reviews, and although it is our best seller, I wouldn’t say it’s our best guitar. The Grand Cutaway is our biggest guitar, so it has the best sound while having the same benefits as our other instruments.”
What fuels your ambition to create an expansive line?
Adam: “We always had a vision of becoming the carbon-fiber instrument company. After making our first few instruments, we learned that we had developed the capability to make practically anything out of carbon, and that capability was our most valuable asset.
“So in 2023 we decided that we would launch eight more instruments based on the top requests from prospective customers. We did that and have plans for seven more in 2024. We’re releasing an A-style mandolin, a 12-string guitar, a classical guitar with or without a cutaway, as well as neck replacements for Fender basses in three sizes – four-, five-, and six-string – plus a baritone electric guitar. After that we’ll slow down a bit on new instrument launches and focus on growing the existing product lines.”
What are you most excited about?
Adam: “We’re extremely excited for the mandolin. The response from the mandolin community has been incredible. Everyone has been so positive, and honestly, nobody questions the logic of using carbon fiber. Everyone just gets it. A mandolin has eight steel strings, so it has a huge amount of tension on the soundboard, making it hard to make a good-sounding wooden one that won’t break simply from passive string tension.”
What are some company goals and individual thoughts you both have as Klos moves forward with these new instruments?
Adam: “More than anything, we want to keep spreading the word. We know that we’re still a tiny brand compared to the big guys, but we also know that many players want a unique instrument from a smaller company that pays close attention to each customer. We’re continuing to reach out to good retail stores and to keep finding good partners who are interested in selling innovative gear that their customers want sold locally.”
Ian: “Passionate guitarists always wish they had more time to play and practice. The worst thing is when you go on a trip and don’t have a guitar on hand to fill in your spare time. I always had the mentality that my guitar is made to be used, and not babied. I was the guy who would put my guitar in a couple layers of garbage bags and shove it in the front of my kayak.
“That attitude is at the core of our vision, to make guitars that are treated more like a piece of gear than a piece of fine art, or delicate furniture at grandma’s house. Once a guitarist gets a Klos guitar and embraces this same vision, it changes your relationship with your guitar. It will never sit in its case. It will always be leaning against your couch, ready to be played.”
- For more on Klos Guitars, visit the company's website.
Jimmy Leslie has been Frets editor since 2016. See many Guitar Player- and Frets-related videos on his YouTube channel, and learn about his acoustic/electric rock group at spirithustler.com.
“Gibson had lost the recipe — not only for guitar building but for making pickups based on their original design.” How Larry DiMarzio’s pickup revolution defined the sound of 1970s guitar rock
“Tariffs on products from its Mexico and China facilities would increase operating costs by $20 to $25 million.” Fender's credit rating is downgraded as tariffs pose new challenges for the guitar and gear maker