Electric Guitar Necks: the Basics
Get the lowdown on materials, truss rods, scale lengths and joints with this simple guide.
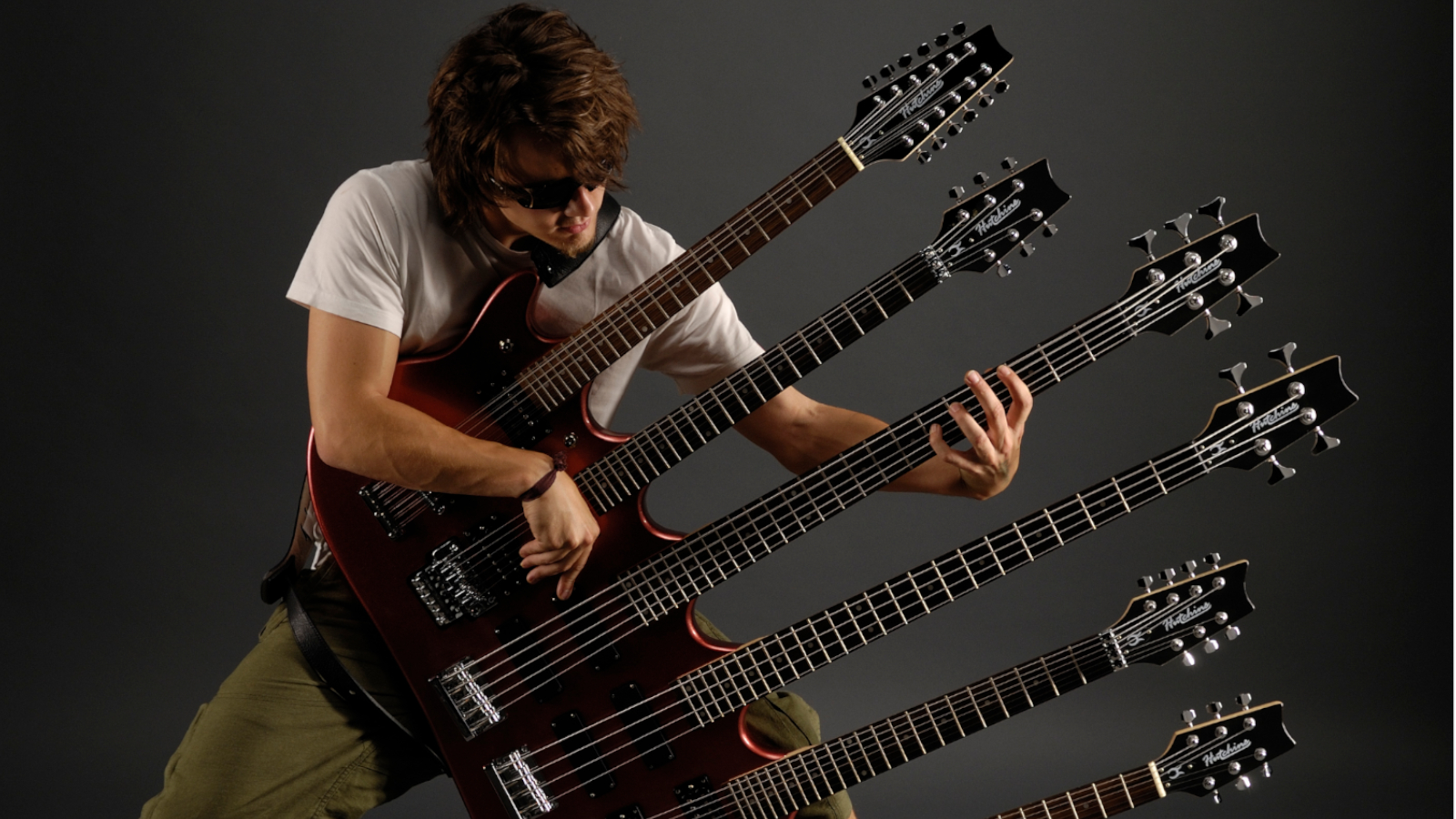
The neck of an electric guitar helps shape the instrument's acoustic voice. It is a primary tonal component, along with the body, bridge, fingerboard, and strings.
Differences in wood density and stiffness alter the way the neck translates string sound to the body.
Tone can vary greatly, even among necks of the same wood type. In most cases, harder materials such as maple produce a bright, clear sound. Mahogany and other softer wood impart more warmth.
You can find alternatives to traditional neck woods more easily today than in the past. Pau ferro (ironwood), rosewood, wenge, and fiber-composite necks are readily available on custom and production instruments.
Truss Rods
Within most necks lies a hidden tone component – the truss rod.
Primarily designed to counter string tension, the truss rod system alters the neck's mass and stiffness.
It must always be under tension: a loose rod can resonate sympathetically with the strings, absorbing some frequencies and causing dead notes and weak sustain.
Get The Pick Newsletter
All the latest guitar news, interviews, lessons, reviews, deals and more, direct to your inbox!
Two common designs are the two-piece double expanding rod and the single rod. A double expanding truss rod's stiffness and weight improves sustain. The single rod weighs less, which helps create a warmer tone.
Scale Length
Scale length is the string's speaking length from nut to saddle. The two traditional scales for solidbodies are 24 3/4" (Gibson) and 25 1/2" (Fender).
In addition to determining fret spacing on the fingerboard, scale length influences a guitar's overall timbre.
Many perceive 25 1/2"-scale guitars as sounding brighter and more transparent than 24 3/4" instruments, along with a sense of definition, cleaner bottom end and more clarity in the high notes.
The two traditional scales for solidbodies are 24 3/4" (Gibson) and 25 1/2" (Fender)
According to other players and builders, the 24 3/4"-scale length imparts a strong midrange kick, delivering a "tight" sound with strong punch and warmth along with a precise, articulated sound.
Several manufacturers build professional quality guitars with scale lengths between 22" and 24 1/2".
The short-scale neck's closer fret spacing facilitates fingering for some players, and shorter string length imparts a chunky midrange quality to the overall tone.
At least one solidbody builder uses a 25"-scale length. "I chose it for feel," said Paul Reed Smith. "It sounds good and is comfortable for players used to the tension of either 24 3/4" or 25 1/2" scale."
Traditional bolt-on solidbody guitars used a 25 1/2"-scale length; likewise set-in neck designs historically featured the 24 3/4" scale.
For decades, guitar makers have created many hybrids of body style, neck/body joints, and scale length, so it's no longer practical to guess the scale length of a guitar by checking its design and features.
When in doubt, whip out a ruler and measure the string's speaking length.
Bolt-On Neck
The way a neck attaches to the body colors a guitar's voice. String vibration transfers to the body through the neck/body joint (as well as through the bridge).
Screws or bolts connect a separate neck and body to produce a bolt-on guitar, such as a Stratocaster or Telecaster. A good fit is critical.
For a bolt-on to have the best possible tone, the neck must fit tightly in the pocket and make good contact on all sides of the joint. Any gap will result in lost sound.
Neck-through-Body
A neck-through-body construction means the neck section continues all the way from the headstock to the strap button; small "wings" glued to the sides form the body.
Neck-through instruments work well in high-volume playing situations that call for definition and clear low end.
Some neck-through guitars such as Gibson's reverse Firebird models (see above), use a laminated mahogany neck section.
Set-Neck
Set-neck construction refers to gluing the neck to the body, as with a Les Paul.
Some builders feel a set-in joint gives the guitar a "singing" quality – notes seem to swell after the pick attack until they reach their final amplitude.
Smooth, warm sustain with moderate attack are characteristics often attributed to set-neck guitars.
Guitar Player is the world’s most comprehensive, trusted and insightful guitar publication for passionate guitarists and active musicians of all ages. Guitar Player magazine is published 13 times a year in print and digital formats. The magazine was established in 1967 and is the world's oldest guitar magazine. When "Guitar Player Staff" is credited as the author, it's usually because more than one author on the team has created the story.
Guitar Center's Guitar-A-Thon is back, and it includes a colossal $600 off a Gibson Les Paul, $180 off a Fender Strat, and a slew of new exclusive models
"We tried every guitar for weeks, and nothing would fit. And then, one day, we pulled this out." Mike Campbell on his "Red Dog" Telecaster, the guitar behind Tom Petty & the Heartbreakers' "Refugee" and the focus of two new Fender tribute models